In recent years, the construction industry has faced a labyrinth of challenges, from towering demand to sticky supply chain issues, which have stretched the timelines for residential builds and reshaped the landscape of home construction. These hurdles have compelled professionals and homeowners alike to navigate a new reality, where delays are expected, and flexibility has become a cornerstone of project planning. Let’s examine the intricate tapestry of the construction supply chain, unravel the issues currently binding it, and stitch together solutions that hold promise for a more resilient future.
The pandemic continues to reverberate through the construction supply chain, altering how we source and use building materials. We’ll examine the reasons for supply chain issues, which products have been impacted, and the ripples they cause throughout a project. On the brighter side, we’ll redefine what sustainability means in the construction context—highlighting its role not just in environmental stewardship but as a keystone in building a supply chain that can withstand the tests of time and policy.
2024 Building Supply Chain Issues
More than four years later, the construction industry continues to grapple with supply chain shortages that began cropping up during the 2020 pandemic. With any system as complex as the building materials supply chain, these challenges are interconnected, often intensifying one another. Here are just a few of the major factors in construction supply chain disruptions that both professionals and homeowners are impacted by:
In 2020, the global market for raw materials, which once accounted for more than 50% of building needs, declined sharply as countries closed their borders and sent workers home. This in turn put more demand on local suppliers and quickly resulted in supply chain shortages.
At the same time, distancing requirements to help stop the spread of Covid-19 meant many construction companies and contractors were out of work. And while those restrictions no longer apply in 2024, businesses are still struggling to regain their workforce. For the past two years, the construction industry has held a 4.6% unemployment rate, higher than the 3.8% national average. To meet employment demands, the industry will need to hire an additional half a million workers on top of the normal hiring rate.
Both challenges come back to an increased demand for construction services. Not only is America short around 3.2 million homes, but people also began spending much more time at home during the pandemic. Remote work has continued into 2024 and homeowners are prioritizing offices, workout spaces, and more in their spending.
All this and more have come together to cause 2 main supply chain issues: higher prices and longer acquisition and project completion times. Construction input costs are up nearly 39% compared to 2020. Before Covid-19, building materials like steel and timber were typically delivered to project sites within two to four weeks of ordering. Now, those materials can take 12 to 16 weeks to arrive. From 2020 to 2022 the average time to completion of a single family home went from 6.8 months to 8.3.
The insulation sector has felt these shocks particularly acutely. Fiberglass, a staple of the industry, has faced shortages due to factory slowdowns and increased demand, a byproduct of the heightened focus on energy efficiency. Some fiberglass and sprayfoam manufacturers also suffered from sourcing raw materials from overseas. Cellulose insulation, reliant on recycled paper feedstock, has been hit by fluctuations in recycling patterns and consumer behavior. Meanwhile, mineral wool has butted against emissions quotas that limit production capacity.
Source: https://www.timberhp.com/building-supply-chain-sustainability
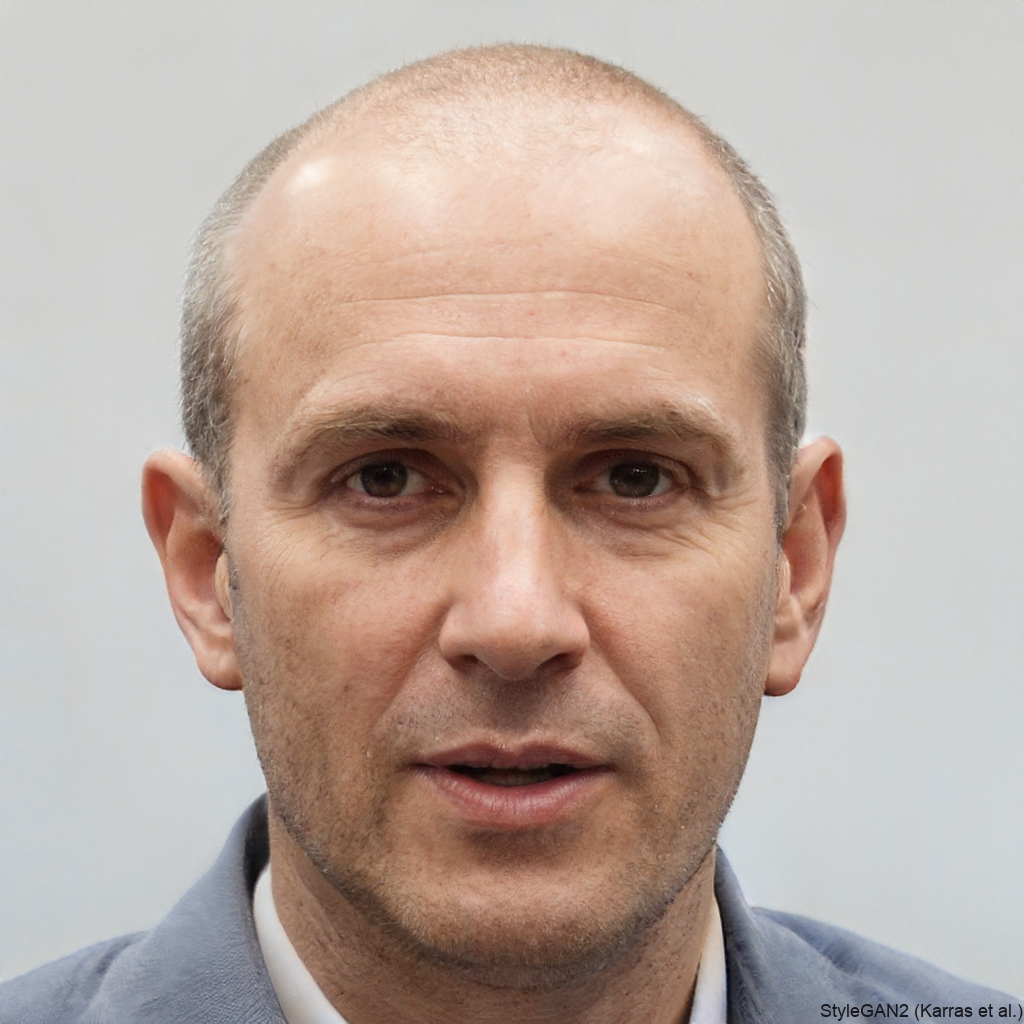
Mr. Nielsen is known for his lyrical prose style and exploration of themes related to memory, family dynamics, and the American South. With [number] years of hands-on experience, Kearns brings a wealth of knowledge to his writing. His ability to break down complex roofing concepts into clear and concise language makes him a valuable resource for both industry professionals and homeowners. Kearns is passionate about staying up-to-date on the latest industry trends and technologies, ensuring his readers have access to the most current information.